Home » Cleaning Services
Category Archives: Cleaning Services
How to Keep Your Apartment Carpet Clean
Carpets add a comfortable and homey feel to any apartment. They also offer sound absorption and heat insulation. This makes them a popular choice for landlords. However, they can become dirty over time.
Some tenants may try to convince their landlords to clean their apartments carpet by bringing up the issue during a walk-through. But it is important to make a formal repair request in writing. Contact Apartment Carpet Cleaning El Dorado Hills CA now!
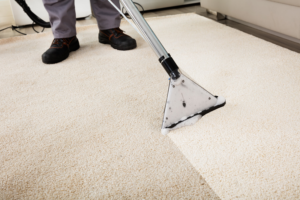
Carpets are a staple in many rental properties. As such, they are prone to wear and tear, especially if they are used by a large number of people. This is why it is important to get them professionally cleaned on a regular basis, usually at least once per year. This will help protect the carpet and keep it in good condition.
Landlords are not required to clean carpets between tenants unless it is specified in the lease agreement. However, they can hire a professional company to do so if the carpet is in poor condition and needs to be cleaned before the new tenant moves in. If a landlord has to do this, they can deduct the cost from the security deposit.
If the landlord doesn’t have the time to do this themselves, they can also opt to use a steam cleaner. This is a cheaper option, but it can take a long time to do the job. The results will not be as good as those from a professional cleaning company, so it is best to leave this job to the professionals.
Whether or not the landlord has to pay for cleaning the carpet between tenants depends on the state law and the lease agreement. For example, some states make it illegal to include a clause in the lease agreement that requires the tenant to pay for routine cleaning of the carpet. If a landlord is going to charge the tenant for cleaning the carpet, they should be sure to document the charges and provide proof that they were incurred.
Rips and stains are not normal wear and tear. They are a sign of damage and should be paid for by the tenant. Tenants should always try to work with their landlords, but if they cannot agree on something, they should move out of the property.
In addition to having to clean the carpet, a tenant may have to pay for the replacement of items like furniture. This can be a big expense and can be difficult to cover with a security deposit. It is a good idea to discuss these issues with your landlord before moving in and to keep records of any repairs or cleaning that you need to do. In most cases, if you bring up these issues in a calm and respectful manner, your landlord will be more than willing to work with you. This way, you can avoid any unnecessary costs and have a pleasant relationship with your landlord.
It is the tenant’s responsibility
A landlord may deduct money from a tenant’s security deposit to pay for cleaning the carpet after he or she moves out. However, this deduction must be justified and in accordance with the law. This means the landlord must provide impeccable records and a clear inventory of the property. In addition, a tenant can use the services of a professional cleaning company for this purpose. However, they should ensure that the service is properly documented and that there are no disputes over any charges.
Most state laws stipulate that a tenant is responsible for cleaning the apartment’s carpets. These laws look at the original condition of the carpet at the time of move-in and then decide whether or not a certain damage is normal wear and tear or a result of a tenant’s actions. This is a very complicated process, and landlords should be careful not to overcharge their tenants.
If a tenant makes a mistake on the carpet, such as spilling a glass of wine, it is best to clean the stain before it becomes a major issue. In most cases, landlords will not charge a tenant for such mistakes. However, if the stain is too large, a landlord may be able to deduct the cost of carpet cleaning from the tenant’s rent.
In the event of a dispute, it is important for both the tenant and landlord to understand their rights. If a landlord attempts to make unjustified charges, the tenant can fight back with legal support from a reputable attorney. Landlords can also hire a reputable firm to clean the carpets, which will save them time and money.
A common concern among tenants is that their landlords will not clean the carpets before they move out. This can be a major headache for both parties, and it is important to avoid such situations by conducting detailed tenant screening with background checks. This will help to prevent a tenant from bringing in pests or other problems that could harm the carpets. It is also important to keep the landlord informed about any problems that could arise, so he or she can address them promptly. This will prevent the landlord from being taken advantage of by unscrupulous tenants.
It is the landlord’s responsibility to repair
Keeping your apartment carpet clean is important to maintain the value of your home and protect yourself from allergies. Dirty carpets can cause a lot of problems, including making your living space less comfortable and creating a health hazard for your family. Fortunately, there are many products available that can help you keep your carpets clean. Many of these products are designed to remove stubborn stains and can be purchased at your local hardware store or online. Some of these products are also available in spray form, so you can apply them to your carpets without having to use a vacuum cleaner.
If you are moving out of an apartment, you should thoroughly clean the carpets before you leave. This will ensure that the landlord can refund your deposit and will prevent you from getting into any unnecessary disputes. You can start by sweeping and vacuuming, then move on to the more difficult tasks like shampooing the carpets. If you are unsure how to do this, you can hire a professional cleaning service to take care of it for you.
Generally, a landlord cannot charge tenants for the cost of cleaning apartment carpets because it falls under normal wear and tear. However, if the carpet is severely dirty and damaged, then it may be worth taking money from the renter to have it repaired. This is not something that a landlord can just deduct from the renter’s security deposit, so it is important for the tenant to keep track of all repairs they need to make.
A tenant should always get all of their issues with the apartment in writing so that they can be dealt with as quickly as possible. If they don’t do this, then the landlord may simply ignore them and not repair them. A verbal conversation is usually the best option, but if this does not work then a written request should be made.
During a walk-through of the apartment, the landlord discovers that the tenant did not clean the carpets before leaving. The landlord then decides to deduct the costs of the carpet cleaning from the renter’s security deposit. This is not allowed under the law. A landlord should only withhold money from the deposit if the tenant is at fault for the damage to the carpet. However, it is important for a tenant to keep a record of all repair requests so that they can be presented if they ever need to. If this is done correctly, the landlord will usually comply and fix the problem as soon as possible. This can save both parties a lot of time and hassle in the future.
Septic Tank Regulations – Legal Requirements For Proper Maintenance
In most states, septic tank professionals must complete specific training courses and pass a certification exam to be able to design or install septic systems. These certifications ensure that the system is designed and installed to meet state regulations and protect environmental resources.
Regulations often stipulate minimum separation distances from septic tanks to residences, wells, and property lines. Check Septic Tank Services Near Me and your local health or environmental department for specific requirements in your area.
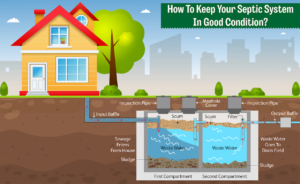
The septic tank is the first step in an onsite wastewater treatment system. The tank collects and stores sewage from the home, separating solid waste from the liquid effluent. Solids that sink to the bottom of the tank become sludge, while scum rises to the surface of the wastewater and floats on top of the liquid waste. The liquid effluent exits the septic tank through a perforated pipe that connects to an absorption field, or leach field.
The septic tank must have adequate capacity to handle the expected load of wastewater from the house, including laundry and garbage disposal waste. The design should take into account the number of bedrooms in the household and any expansion attics. The flow rate and volume of solids in the wastewater will also factor into the septic tank’s capacity.
A septic tank should be constructed from durable materials that are resistant to corrosion, decay, and frost damage. The tank should also be water-tight, and all joints below the liquid level must be sealed and tested.
When a new septic tank is installed, the outlet connections of the tank and each compartment thereof must be provided with either a tee not less than four inches in diameter or a durable baffle. The baffle or tee must be permanently fastened in place and extend below the liquid level by 25 to 40 percent of the total liquid depth.
The septic system must be installed on a site that is free of water and gravel runoff and soil conditions that could cause erosion and movement of the tank or its components. It is recommended that a site evaluation be performed before construction.
It is also important to map out the septic tank and the drain field or mark the location with permanent stakes. This will help homeowners identify and avoid the septic system when working on landscaping, paving, or any other work that may disturb the tank and drain field. It will also help prevent the accidental or intentional damage of septic system components.
Once the septic tank is installed, it is important to backfill the area around the tank and drain the field with soil that will not settle over time. The backfill should be free of clods, large rocks, and frozen matter, and must be amended with crushed rock or pea gravel no smaller than 1/2-inch in size if native material is not suitable.
Maintenance
A septic system requires regular maintenance and responsible operation to preserve its integrity and protect the environment. The state takes this seriously and has strict regulations regarding the design, installation, and management of septic systems to minimize environmental impacts and public health concerns.
All septic tanks have an opening that waste flows through, known as the outlet. A septic tank’s lid is usually secured by a grate to prevent animals or children from entering the septic system and may be locked to discourage tampering. The tank walls must be constructed of strong materials to resist the flow of septic liquid effluent. A septic tank should be pumped regularly to remove solid waste accumulations that are not biodegradable. This is especially important since septic tanks cannot remove all of the wastewater solids that enter the tank, regardless of how well the system operates.
Typically, the septic tank has a PVC “T”-shaped fitting with a short section of horizontal piping leading into a slightly longer vertical section. The bottom of the vertical section must extend several inches below the scum layer. The liquid waste in the septic tank is forced through this outlet to a distribution box or an absorption field for continued treatment.
The distribution box contains perforated pipes that distribute the liquid waste from the septic tank evenly throughout a drain field or seepage pits. The distribution box and the absorption field or seepage pits must be properly sized and constructed to ensure that the system functions correctly and does not pose a risk of environmental pollution.
Besides proper system construction, the maintenance of a septic system includes regular inspection by a professional inspector. These inspections are necessary to check for the proper functioning of the septic system and to detect any potential problems, such as clogging or leaks. Inspectors should look for signs of sludge buildup in the septic tank and ensure that the absorption fields or seepage pits are adequately sized and located to avoid contamination of groundwater or nearby surface water bodies.
Inspection
If you own a home with a septic system, it’s important to stay on top of inspections and certification. This not only ensures that the septic tank, drainfield, and leach field are safe, but also helps keep your home’s value up.
Generally, inspectors will check three elements of the septic system: the septic tank, the distribution box, and the leach field. They’ll look at the septic tank to make sure there are no cracks, leaks, or structural problems and that it isn’t too full or too empty. They’ll also look at the leach field to see if it is well-spaced and properly sized, and that there are no clogs or leaks.
A septic tank must be inspected every two to three years. When your septic tank needs to be pumped, it’s a good idea to use a licensed septage waste transporter (septic pumper). They can inspect the septic tank and determine how much material is in it. They can also help you keep a record of all the pumping and inspections and any maintenance and repairs that are required.
In addition to looking at the septic tank and its components, an inspector will check for other problems such as a soggy yard that’s wet all the time, lush vegetation, or standing water in the drainfield area, as these may indicate a septic system problem. They’ll also look at the D-box, or distribution box, for problems such as damaged outlets that restrict flow, or a tilting or tipping that causes uneven distribution of wastewater.
In the state, septic system professionals are required to pass written, oral, and practical examinations before they can be certified by the State Sanitary Code. This certification demonstrates that they have a thorough knowledge of how to design and install on-site septic systems that meet environmental protection standards, especially in ecologically sensitive areas. Homeowners should verify their septic system designers and installers are certified, and ask for recommendations and reviews before hiring them. They should also check with their local health departments to learn if there are any additional regulations governing the installation, inspection, and maintenance of on-site septic systems in their area.
Certification
Septic tank professionals must pass a rigorous exam to become licensed to install or repair septic systems. The exam covers minimum site conditions, construction criteria, appropriate connections and venting, wastewater disposal, and safety considerations. Licensed septic system professionals can help customers choose the right septic tank for their property and help them maintain their septic system to ensure proper operation and prevent potential problems.
Septic tanks are essentially settling chambers that allow time for scum and sludge to separate from wastewater, so clear liquid can flow into the drainfield or pump tank. A septic tank is typically required to have a capacity of at least 1,000 gallons for a single-family dwelling. For multiple-family homes, the tank size increases by 125 gallons for every additional bedroom.
The tank must be constructed of sound and durable materials that are resistant to corrosion, decay, or frost damage. It must also be watertight and free of cracking, leaking, or buckling due to settlement or backfilling. An inspection port that extends to the finished grade must be provided for each tank inlet and outlet, except for outlets where a baffle, septic solids retainer, or effluent filter is used. These must be directly below the manhole, and the manhole cover shall be a secure, bolted, or locked lid.
A septic tank should be located on a level, well-draining site with a suitable soil type. The septic tank should be at least six feet away from any structure and within three feet of the property line. The tank should be surrounded by a backfill that is free of large stones, roots, and other foreign objects and thoroughly tamped.
The absorption field is a series of trenches or distribution pipes that are filled with washed gravel, stone, or a graveled product where the wastewater is biologically treated by the soil. It is important to properly size and install the absorption field, as the wrong material can lead to costly repairs and system failure.
Homeowners can reduce the load on their septic system by using water efficiently, fixing leaky fixtures, and being cautious about what goes down the drains. They can also help the system work better by getting regular septic tank pumping and by having their septic system inspected by a professional, who can catch any problems early on.
Insulation Remover – How Much Does it Cost to Remove Old Insulation?
Replacing old insulation can be a very effective way to make your home or business more energy efficient. However, removing the old insulation can be a messy and time-consuming project.
Whether you’re a DIYer or hiring a professional, there are several things to consider when it comes to tackling this task. For more information, click the Perth Insulation Remover to proceed.
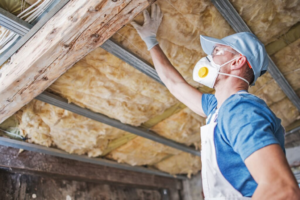
Insulation is vital for energy efficiency in both homes and businesses. However, it can become damaged by pest infestations, moisture damage, and general wear and tear over time. When this happens, it’s important to remove and replace the insulation. This will improve energy efficiency and prevent health risks.
Before beginning the removal process, it’s crucial to clear the work area of furniture and other objects that could be in the way. This will prevent injuries and make the process easier. You can also cover floors and surfaces with drop cloths to protect them from debris and insulation particles during the process. Lastly, you should purchase personal protective equipment (PPE) such as goggles, gloves, and a mask to protect yourself from irritation.
Depending on the type of insulation you have, there are several different ways to remove it. You can use a knife or foam saw to cut through the insulation and pull it away from the wall or ceiling, or you can use a vacuum cleaner with a HEPA filter. It’s recommended to wear PPE when removing old insulation, as it may contain mold spores and dust that can cause allergies.
Some types of insulation, especially spray foam, are flammable and require special handling and disposal procedures to minimize fire hazards. It’s best to hire a professional with the right credentials and equipment for this task. Additionally, some older insulation materials are contaminated with toxic substances like asbestos, which can cause respiratory problems when inhaled.
The insulation removal process is a messy and inconvenient job that requires proper safety measures to avoid injury or health problems. If you have a large project that involves changing walls, ceilings or floors, it’s a good idea to call in a professional insulation removal company. They will handle the job safely and efficiently.
Insulation can be made from a variety of materials, including fiberglass, rock and slag wool. It can also contain dangerous chemicals such as formaldehyde, asbestos, and other carcinogenic substances. The best option is to hire a professional insulation removal company that will take care of the hazardous materials and ensure that they are disposed of properly. They will also follow strict safety protocols to protect themselves and your family from exposure to harmful contaminants.
Tools
If your attic was previously insulated with Blown Cellulose or Fiberglass Batt Insulation, then a large amount of material will need to be removed from the area before new insulation can be installed. If this is the case, then it will be necessary to use a special vacuum system that will allow you to remove the old insulation without spreading it throughout your home. In addition to a professional vacuum system, you will also need some special tools to help with the process of removing insulation.
A wire stripper is a tool that can be used to remove insulation from a wire or cable. This tool generally has a pair of opposing blades that can be closed together to cut the wire or cable. It can then be used to peel the insulation off of the conductor and remove any remaining adhesive. It is recommended that you wear a face mask and gloves when using this tool.
There are a number of different types of wire strippers available on the market. The different variations differ in appearance, handle size and shape, handle coating (often rubberized to protect against electric shock), and the number and size of notches that are built into the tool. However, all of the different versions of this tool perform the same function.
To use the wire stripper, first position it on the end of a piece of wire and close the jaws around it. Then, slowly press the handles together to cut through the insulation on the wire. Be sure not to press too hard, as you could accidentally nick the metal conductors underneath.
Another type of insulation removal tool is a screwdriver-like device that has one or more screw-in prongs at the base of the handle. It is designed to pierce through the outer layer of insulation and expose the copper core. It is then possible to use a wire stripper to remove the rest of the insulation from the conductor.
This tool is designed to remove bonded insulation from medium voltage cables, including XLPE and EPR. It can be adjusted to fit a variety of wire sizes and is easy to operate.
Time
If the old insulation in your home is moldy or water-damaged, it may be a health hazard that needs to be removed. This process requires tearing down the drywall in the affected areas and disposing of the damaged materials and any contaminants that have been exposed. It is a demanding DIY project that must be performed by someone who is familiar with the process and adheres to strict safety measures.
The most common kind of insulation in homes today is blown-in fiberglass or cellulose. This is more difficult to remove than batting, but it can be done if you have the proper equipment and professional assistance. The first step is to prepare the area. Cover up any items in the living room, put down a drop cloth or plastic sheeting, and clear a path to your attic access door. You can also wear protective clothing and a dust mask to prevent inhaling any contaminants.
You’ll need a powerful insulation removal vacuum with a HEPA filter. This device will quickly suck up the contaminated materials and transport them into a large garbage bag for disposal. Make sure it has a long extension hose and can handle the volume of materials that will need to be removed. You’ll also need a sturdy ladder to reach high attic spaces safely and heavy-duty garbage bags. You should also have a partner to help you carry full bags and transport them to your vehicle for disposal.
When removing blown-in insulation, you’ll want to work in small sections. This will give you a better chance of keeping the contaminants contained to one small area rather than spreading them throughout your entire house. It will also reduce your risk of inhaling contaminated dust and mold spores.
It’s important to take your time during this process. If you rush, you could wind up with a mess that will take more time to clean up. Once you’re finished, remove the empty bags from the attic and discard them in a dumpster outside your home. Alternatively, you can use a spray foam insulation to replace the existing blown-in insulation in your walls. This is a more environmentally friendly alternative that will save you the time and hassle of tearing down your walls. It can also be completed in a day, making it less disruptive than a complete drywall teardown.
Cost
Insulation can be a major investment in your home. However, there are many benefits to having insulation installed in your home, including lowering energy bills and making your home more comfortable. In addition, you can also boost your home’s resale value. But how much does it cost to have insulation installed? The answer to this question varies depending on the type of insulation, the amount of insulation, and the installation process.
Insulation is material designed to prevent heat or sound from passing through walls and ceilings. It can be made of a variety of materials, and it is used in homes to help reduce their heating and cooling costs. There are many different types of insulation, and each one has its own unique characteristics. Some are more environmentally friendly than others, while some are more expensive to install.
The cost to remove and replace insulation varies widely, but in general the average cost is about $900 for an attic with about 600 square feet of space. It is important to remember that this price does not include the cost of installing new insulation or any other related expenses, such as disposal or roof repairs.
If you are considering replacing your existing insulation, it is best to work with a professional. They can provide a quote for the entire project and ensure that the job is completed safely and effectively. In addition, they can also advise you on the most suitable type of insulation for your home.
Other factors that can influence the cost of removing and replacing insulation include:
Blown insulation – This type of insulation is blown into the attic using a machine. It is more efficient than fiberglass batting, but it may be more difficult to install. It can be a good option for older homes that have old blown insulation that needs to be removed.
Moldy insulation – Old and moldy insulation can be a serious health risk. It can harbor allergens and other pollutants that can damage your indoor air quality. Moldy insulation should be replaced immediately to avoid further damage and to protect your family’s health.